The Evolution and Importance of Electric Plastic Injection Moulding Machines in Metal Fabrication
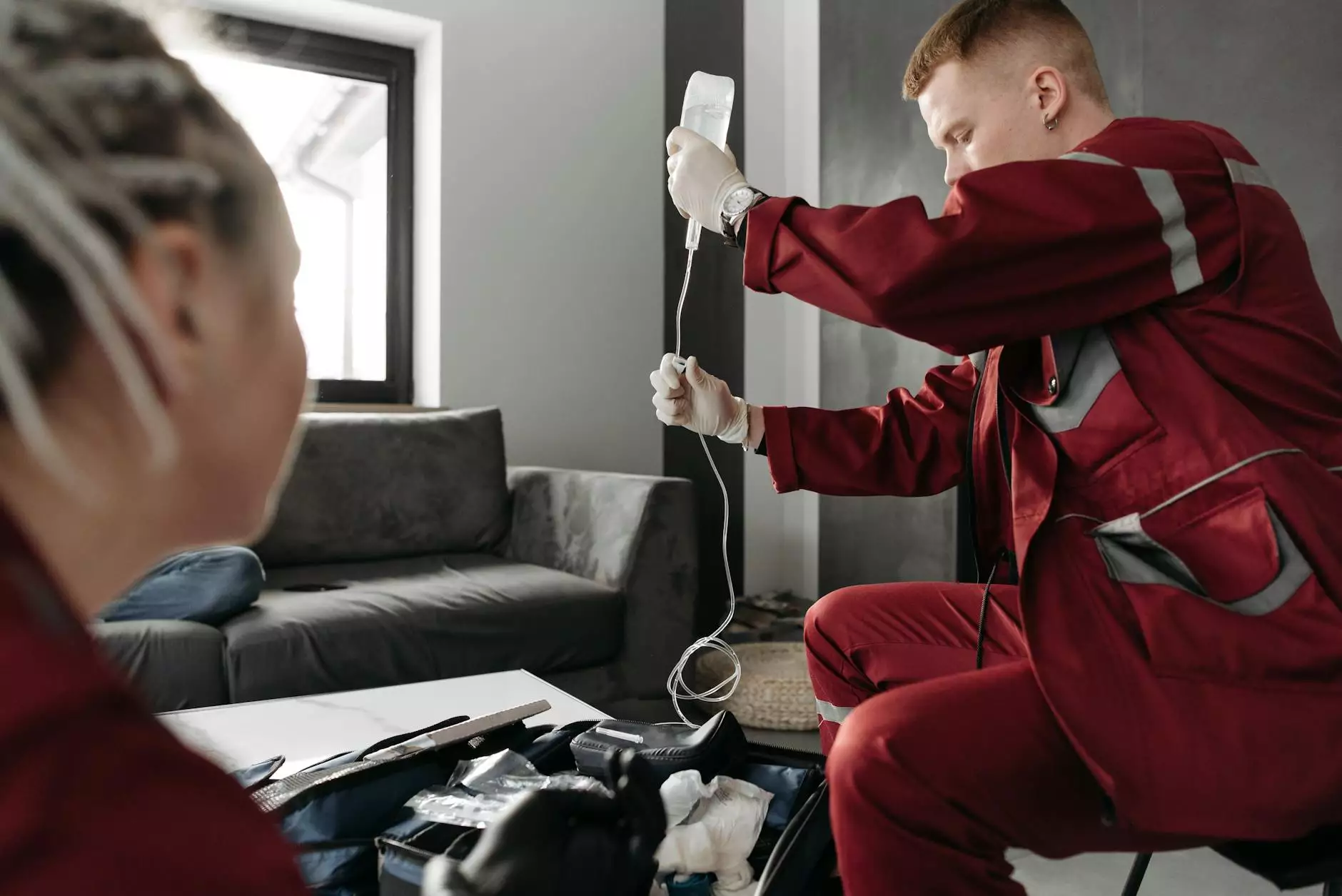
The world of manufacturing has seen a profound transformation over the last few decades, particularly with the rise of innovative technologies that have redefined how products are created and processed. Among these key technologies, Electric Plastic Injection Moulding Machines stand out due to their efficiency, precision, and environmental advantages. As we delve into this article, we will explore the significance of these machines, their applications in the metal fabrication industry, and the future trends shaping this technology.
Understanding Electric Plastic Injection Moulding Machines
Electric Plastic Injection Moulding Machines are highly sophisticated pieces of equipment designed to produce plastic parts with exceptional accuracy and repeatability. Unlike traditional hydraulic systems, these machines utilize electric motors for the injection process, leading to numerous benefits that make them the preferred choice in modern manufacturing. Let’s break down the core components and functioning of these machines:
Core Components
- Injection Unit: Responsible for melting plastic pellets and injecting them into the mould.
- Clamping Unit: Holds the mould components in place during the injection process and ejects the finished part.
- Control System: Regulates temperature, pressure, and speed, ensuring optimal cycle times.
- Electric Motors: Provide high speed and precision, enabling efficient production runs.
How They Work
The process begins with raw plastic pellets being fed into the injection unit, where they are heated until liquefied. The molten plastic is then injected into a clamped mould under controlled conditions. As the plastic cools, it solidifies, forming a precise part that is later ejected from the mould. This seamless process allows manufacturers to produce complex shapes with minimal waste and high repeatability.
Advantages of Electric Plastic Injection Moulding Machines
Choosing an Electric Plastic Injection Moulding Machine over traditional hydraulic models comes with a plethora of advantages, which we will outline below.
1. Enhanced Precision
Electric machines are known for their exceptional precision due to the use of servo motors, which provide consistent and repeatable control over the injection process. This precision reduces the likelihood of defects and enhances overall product quality.
2. Increased Energy Efficiency
Energy consumption is a significant concern in manufacturing. Electric machines consume less energy compared to hydraulic versions, leading to lower operational costs. Their energy savings can reach up to 50%, making them a sustainable choice for the environment.
3. Reduced Cycle Times
Due to the rapid response times of electric motors, the cycle times of Electric Plastic Injection Moulding Machines are significantly shorter. This efficiency allows manufacturers to increase production rates and meet growing market demands without compromising quality.
4. Environmentally Friendly
These machines generate less noise and emissions, contributing to a healthier workplace and a cleaner environment. Their enhanced efficiency in energy use further solidifies their status as a sustainable manufacturing solution.
5. Lower Maintenance Needs
The robust design and fewer moving parts in electric machines result in lower maintenance requirements, reducing downtime and maintenance costs. This reliability is crucial for businesses seeking to maximize productivity.
Applications in the Metal Fabrication Industry
The versatility of Electric Plastic Injection Moulding Machines allows them to be used across various applications in the metal fabrication industry. Here are some notable examples:
1. Automobile Parts Manufacturing
The automotive industry is one of the largest consumers of injection-moulded plastic components. From dashboards to bumpers, electric machines play a crucial role in the production of lightweight, durable parts that enhance vehicle performance and fuel efficiency.
2. Consumer Electronics
With the rapid advancement in technology, the demand for compact and efficient consumer electronics has surged. Electric Plastic Injection Moulding Machines facilitate the production of intricate plastic casings and components that are essential for devices such as smartphones, laptops, and home appliances.
3. Medical Equipment
The medical industry requires products with stringent quality standards. Electric machines provide the necessary precision and cleanliness required for manufacturing components in medical devices, ensuring the safety and effectiveness of healthcare solutions.
4. Household Items
From kitchenware to cleaning products, many everyday items are produced using injection moulding. The efficiency and cost-effectiveness of electric machines enable manufacturers to produce high-quality household products that meet consumer expectations.
5. Packaging Solutions
The packaging industry has also benefited from the capabilities of electric injection moulding. These machines are used to produce robust, lightweight, and space-efficient packaging solutions that help in minimizing material waste.
Future of Electric Plastic Injection Moulding Machines
As the demand for sustainable and efficient manufacturing solutions continues to rise, the future of Electric Plastic Injection Moulding Machines looks promising. Several trends are shaping the industry:
1. Integration with Industry 4.0
The advent of Industry 4.0 has led to greater automation and connectivity in manufacturing. Electric machines are evolving to incorporate advanced technologies such as Artificial Intelligence (AI) and the Internet of Things (IoT). This integration allows for real-time monitoring and data analytics, optimizing production efficiency and predictive maintenance.
2. Design Innovations
Design innovation remains at the forefront, with new mould designs allowing for even more complex shapes and better material utilization. Enhanced simulation software helps in the optimization of designs before production, reducing material waste and improving efficiency.
3. Sustainability Initiatives
As more businesses turn towards eco-friendly practices, the development of bio-based and recyclable materials will influence the designs and operation of electric moulding machines. This pivot towards sustainability will be critical in meeting regulatory requirements and market expectations.
Conclusion
In conclusion, Electric Plastic Injection Moulding Machines represent a critical technological advancement in the field of metal fabrication and manufacturing at large. Their precision, efficiency, and reduced environmental impact not only align with the goals of modern production but also cater to the changing demands of industries worldwide. As we move forward, the continual advancement of these machines will play a vital role in shaping the future of manufacturing, with companies like Deep Mould at the forefront of innovation.
Call to Action
If you are considering upgrading your manufacturing capabilities or are interested in learning more about how Electric Plastic Injection Moulding Machines can revolutionize your production line, Deep Mould is here to assist you. Our expertise in Metal Fabrication and relationship with leading manufacturers ensures that you receive the highest quality solutions tailored to your needs.