Transforming Industries: How a Plastic Tooling Manufacturer Leads the Way
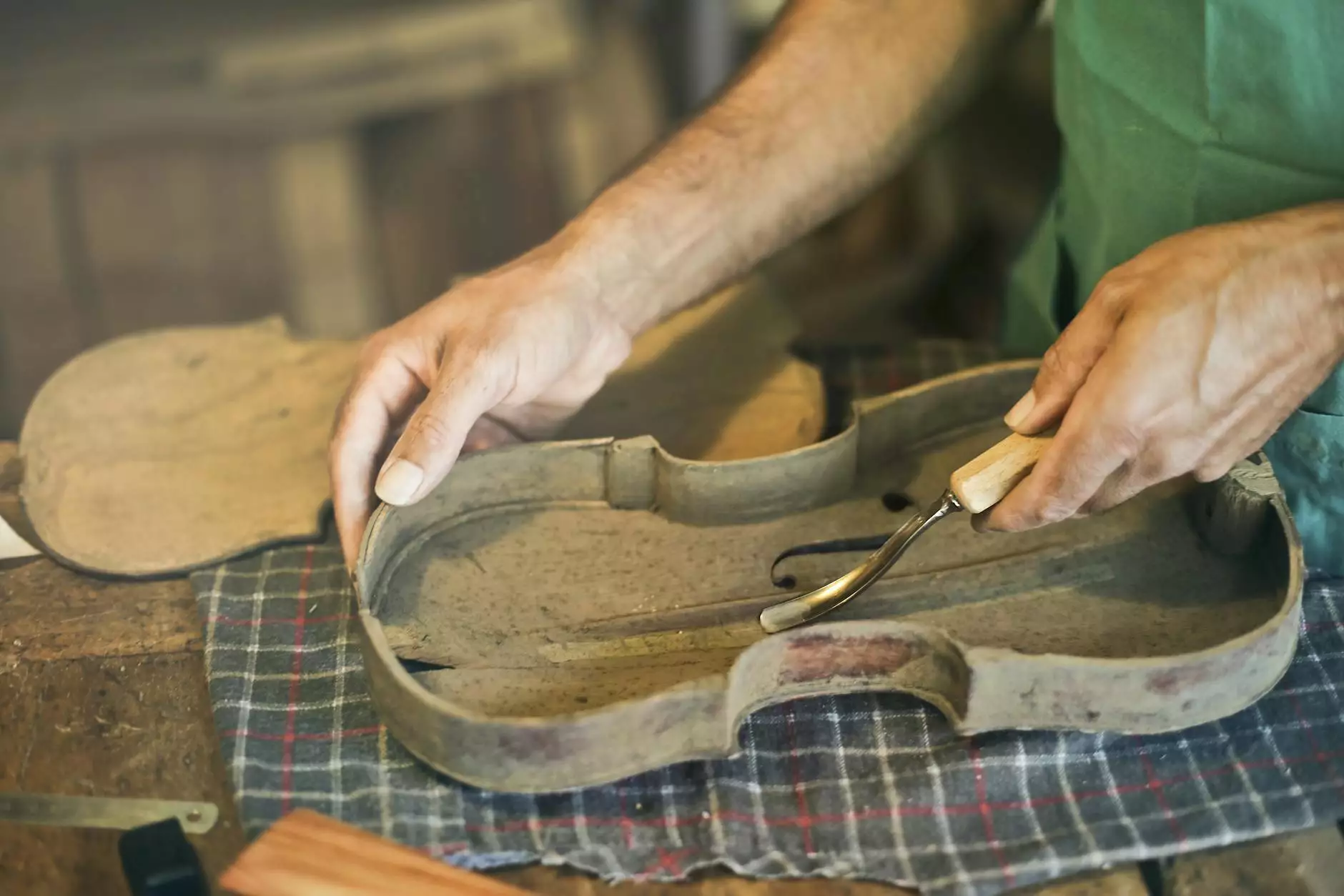
The world of manufacturing is evolving rapidly, and at the forefront of this evolution is the plastic tooling manufacturer. Specializing in creating mold tools and components, these manufacturers play a crucial role in various sectors, including automotive, consumer goods, and electronics. In this article, we will delve into the intricacies of plastic tooling manufacturing, its benefits, and how companies like deepmould.net are setting standards in this competitive landscape.
Understanding Plastic Tooling: A Foundational Overview
Plastic tooling refers to the production of tools that are used to shape and mold plastic materials into a variety of products. This process not only requires precision but also an extensive understanding of materials and manufacturing technology. Let’s break down the primary components involved:
- Molds: The heart of plastic tooling, molds dictate the shape and quality of the end product.
- Materials: High-quality plastic is essential for durability and performance, typically involving thermoplastics and thermosets.
- Machining Techniques: CNC machining CNC (Computer Numerical Control) plays a vital role in creating the intricate designs required in tooling.
- Quality Assurance: Rigorous testing and quality checks ensure that regardless of scale, each product meets industry standards.
The Advantages of Choosing a Superior Plastic Tooling Manufacturer
With numerous options on the market, selecting the right plastic tooling manufacturer can make all the difference. Here are the major advantages of opting for an industry leader like deepmould.net:
1. Enhanced Precision and Quality
Today’s manufacturing environment demands precision. A top-tier manufacturer utilizes state-of-the-art technology that ensures each product meets exact specifications. Employing advanced techniques and machinery, they guarantee a flawless final product that leads to decreased waste and increased efficiency.
2. Customization and Flexibility
Different clients have distinct needs. Leading plastic tooling manufacturers offer tailored solutions, allowing for bespoke designs that cater to specific applications. This level of customization can significantly enhance user experiences and provide businesses with a competitive edge.
3. Fast Turnaround Times
In the fast-paced world of manufacturing, time is of the essence. Efficient processes and streamlined communication channels enable a quick turnaround on projects without sacrificing quality. Companies like deepmould.net pride themselves on their ability to deliver products swiftly, ensuring that clients can meet their market demands promptly.
4. Expertise and Experience
Expert teams with years of industry experience contribute to the innovative solutions offered by a plastic tooling manufacturer. The amalgamation of talent and experience results in cutting-edge tooling designs and expert problem-solving capabilities.
The Role of Metal Fabricators in the Context of Plastic Tooling
Metal fabricators are essential in complementing the work done by plastic tooling manufacturers. While the latter focuses on designing tools for plastics, metal fabricators create parts and products often needed in conjunction with plastic components. The synergy between these fields enhances the overall manufacturing ecosystem, enabling the production of complex assemblies that combine both metal and plastic.
Collaboration for Enhanced Manufacturing
The collaboration between plastic tooling manufacturers and metal fabricators leads to stronger products with greater functionality. This strategic partnership can result in:
- Innovative Hybrid Products: Products that combine the durability of metal with the lightweight advantages of plastic.
- Streamlined Production Processes: Coordinated efforts lead to reduced lead times and efficient resource utilization.
- Cost Savings: Joint efforts often result in cost-effective solutions, optimizing both material and labor costs.
Case Studies: Success Stories in Plastic Tooling Manufacturing
To truly appreciate the impact of a proficient plastic tooling manufacturer, let’s look at a few success stories related to deepmould.net:
Case Study 1: Automotive Component Production
In one notable project, deepmould.net partnered with an automotive manufacturer to create a series of lightweight, high-strength components. Utilizing advanced injection molding techniques, they produced components that not only met strict automotive regulations but also offered weight savings of up to 30% over traditional metal parts. This project exemplified how innovative tooling solutions can contribute to overall vehicle efficiency.
Case Study 2: Consumer Product Optimization
A leading consumer goods company sought to redesign its product line to be more sustainable. By collaborating with deepmould.net, they developed molds for biodegradable plastics, significantly reducing the environmental footprint. This partnership underscored the value of innovation in product design to meet consumer preferences for sustainable options.
Key Technologies Transforming Plastic Tooling Manufacturing
The future of plastic tooling lies in technology. As robotics, artificial intelligence, and advanced manufacturing techniques continue to develop, they are transforming how manufacturing is conducted:
1. Additive Manufacturing
Also known as 3D printing, additive manufacturing allows for rapid prototyping and the creation of complex molds that were previously impossible to produce. This technology not only speeds up the development process but also enables the creation of specialized molds for niche markets.
2. Advanced CAD/CAM Software
Computer-Aided Design (CAD) and Computer-Aided Manufacturing (CAM) software streamline the design and production processes. These tools facilitate precise modeling and allow manufacturers to simulate the molding process, ensuring accuracy before production begins.
3. Automation and Robotics
Automated processes enhance efficiency and consistency in manufacturing. With robotics, manufacturing lines can operate with minimal human intervention, leading to faster production and fewer errors.
Future Trends for Plastic Tooling Manufacturers
The industry is on the brink of significant changes, and plastic tooling manufacturers must adapt to stay relevant. Here are some emerging trends to watch:
- Emphasis on Sustainability: As environmentally friendly practices gain importance, manufacturers are increasingly focusing on sustainable materials and processes.
- Increased Customization: The demand for personalized products is growing, leading manufacturers to develop systems for rapid, on-demand customization.
- Integration of AI: Artificial Intelligence is expected to play a key role in optimizing production schedules and improving quality control.
The Conclusion: Partnering with the Best in Plastic Tooling
In conclusion, selecting the right plastic tooling manufacturer is paramount in capitalizing on the numerous benefits that quality tooling can bring to a business. Companies like deepmould.net are leading the way, offering unparalleled services in design, production, and customer support. By embracing modern technologies and maintaining a commitment to quality and innovation, they help businesses—in various sectors—achieve their manufacturing goals. As industries continue to evolve, these partnerships will increasingly become vital for businesses looking to excel.
Get Started Today!
If you’re in search of a reliable and innovative plastic tooling manufacturer, look no further than deepmould.net. Embrace the future of manufacturing and unlock new possibilities for your business today!